
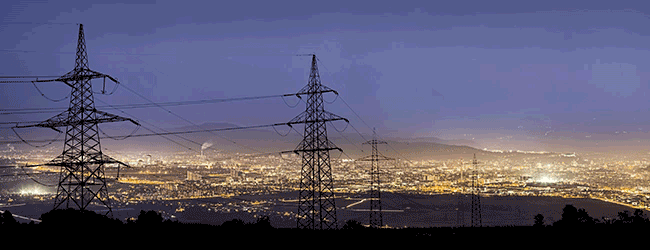
Amp Up Efficiency On Remote Worksites
Working remotely is a big part of the job in the utilities industry. There are many unique challenges remote workers face. Safety and productivity are two of the biggest. But, with the right strategies in place, it’s possible to overcome those challenges. Here are some ways you can reduce cost and increase efficiency at remote worksites.
Prep the Jobsite Work Areas
Make sure your remote work sites are adequately prepped and prepared. You want to keep things moving at a steady pace in order to meet task deadlines. So, take the time to lay out the jobsite for efficiency. For example, once your workers arrive at the worksite, they should store their tools and materials in a convenient, optimal location. If they have to walk long distances back and forth to get these things, they’re wasting valuable time. The hours of unproductive labor time can increase dramatically when this fundamental step is ignored.
Provide On-Site Supervision
It’s a good idea to have a supervisor, or even a crew leader, stationed at each remote worksite. The rest of the team will work more efficiently knowing that there is someone keeping an eye on the operation. This person is also more effective at handling any issues that arise. They can take care of safety incidents, facilitate communication, and answer any questions that might come up. Having a designated person to take the lead and address unplanned situations will increase efficiency on the job.
Improve Safety
Accidents and injuries can be costly to any operation. This is especially true for remote worksites that involve only a few employees. If one person gets hurt, the entire project could be delayed. Improve safety at your remote worksites by implementing a health and safety program for your employees. Make sure they are adequately trained on all required tasks. Provide them with the right gear, supplies and personal protective equipment. Address their concerns and answer their questions about working safely. Accidents and injuries can be devastating to employees. Not only that but it can slow down production and decrease employee morale.
Shops and Garages
Employees who work out of shops and garages play a big role in your company’s operation. They perform preventative maintenance and unplanned repairs. Both are vital aspects of a fleet maintenance program. There are many factors to take into consideration for keeping a fleet maintenance operation productive. Below are some things that will help you reduce cost and increase efficiency.
Set Goals for Your Equipment and Employees
What sort of uptime do you expect with your mobile equipment? Do you always need a certain number of vehicles available? Answering these questions will help you understand what needs to be done to maintain those equipment goals. What about your employees? What level of training do you expect them to have? You might want to consider providing your mechanics with additional training. Both in-shop and vendor training can be useful. Skilled workers will reduce costs by working more efficiently with fewer errors.
Analyze the Operation of Your Shop
As an operations manager, you should routinely analyze your project reports. Doing this can give you insights into areas that could use some improvement. Often times you’ll notice trends. Some good trends and some not-so-good. Regularly monitor your job cost data and equipment health data. That way, any issues you find can be addressed quickly. When reviewing vehicle repair histories, you can identify patterns of fleet vehicles that need repeat repairs. Remember to record this data for easy access in the future. Project and compare your estimated vs. actual repair times, costs, etc. to look for areas of potential improvement. Another interesting analysis you can do is the amount of time that your mechanics spend actually servicing vehicles. You’ll also want to run a cost analysis on things like in-house vs. vendor repairs, and overtime vs. hiring temporary employees.
Keep Work Areas Clean, Safe and Organized
Partly for safety, partly for convenience: keep a clean and organized workshop. Keep cleaning supplies on hand that will improve the health and cleanliness of your employees. All-purpose hand wipes go a long way in boosting morale, productivity, and cleanliness. Keeping items properly stored and easily accessible creates a more enjoyable workplace and instills a sense of pride. When members of your staff can find the tools and supplies they need quickly, they are able to fulfill their tasks more efficiently.
Maintain a Healthy Inventory
It’s not enough to store items properly. Make sure your mechanics always have access to the necessary tools they need for completing their tasks. Keep common and frequently used items in stock. Figure out which critical spare parts you need to have on hand at all times. Maintaining a healthy inventory will reduce the amount of downtime on your vehicles. Which translates to more savings and a more efficient operation of your fleet. And equates to less rogue spend that can greatly impact your bottom line.
Best Practices
Wondering what else you can do to reduce cost and increase efficiency? We’ve got some additional tips that you might find useful.
Empower Your Employees
Allow your team to challenge the way things are done at your workplace. Often times, the “ground-floor” employees have some of the best ideas for process and safety improvements. After all, they’re the ones doing the work day-in and day-out. Ask them for feedback. Get some perspective on what they think is and isn’t working. Some questions you could ask them include:
- Do you think it makes sense for us to do it this way? How would you do things differently?
- Does the equipment we provide allow you to do your job safely and efficiently?
- What are some of the biggest struggles and challenges that get in the way of productivity?
- What are the most time-intensive tasks? How do you think we could speed up the process?
Create a Master Schedule
Increase workplace efficiency by planning the work ahead of time. Planning and scheduling work is a crucial part of any fleet or utility maintenance process. Obviously, things are going to come up and you’ll have to be somewhat flexible. But operating with a master schedule will ensure the least amount of downtime. Consider using software programs for scheduling work.
Focus on Quality
Poor quality work can increase the likelihood of having to repeat the task or project down the road. Rework increases the cost to your company. Think of how much money is wasted in time, parts, and labor. All because the quality of work was not adequate. There are two components of high-quality work performance. The first component is your employees. Make sure you hire skilled workers who are able to perform the tasks of the job. Provide them with additional training when necessary. In fact, even the most experienced workers could use refresher training every once in a while. Also, consider implementing some sort of performance review program. Even if it isn’t anything too formal. You don’t want workers on your payroll who slack off, don’t finish the job, or only put in 50% effort. High quality work comes from high quality employees. The second component is the tools and resources used to get the job done. Do your employees have access to supplies that will enable them to do high quality work? Or are they having to “make do with what they’ve got” instead? It’s hard for workers to do a good job if their tools and resources are old or outdated. Take a look at your inventory. Replace what you need to, and upgrade where you can.
In Review
Operations managers face many challenges. But if you can implement just one or two of these suggestions, you could begin to see a major increase in workplace efficiency. In turn, that will help to reduce cost. Everybody wins when working form a more productive workplace.